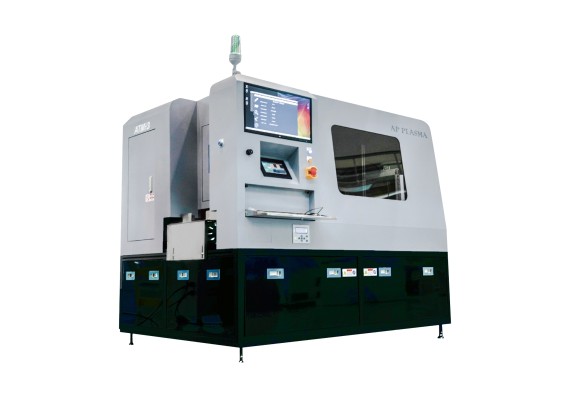
3Dエアオーロラ自動粗加工装置(型番:ATM3)
サイズ: 長さ1860mm × 幅1320mm × 高さ2150mm 製品の特長: (1)消費電力:5kW、CE認証取得済み! (2)操作が簡単なユーザーインターフェース (3)完全自動化システムで、平均処理速度はアッパー1足あたり10秒 (4)世界最先端の高濃度・低温オーロラプラズマ発生装置 (5)内蔵の自動検出・デバッグシステムにより、生産歩留まり100%を実現 (6)独自開発の3Dビジュアルスキャンシステムで、靴型に応じたオーロラスプレーパスを自動計算 応用説明: 従来の靴製造工程では、粗削り、酸・アルカリ洗浄、プライマー処理などの前処理工程が必要であり、これらはその後のアッパーへの接着作業を円滑にするために不可欠でした。しかし、これらの前処理工程は作業者に大量の粉塵による健康被害をもたらすだけでなく、排水汚染や大気汚染といった環境問題も引き起こします。 研究によれば、従来の靴製造におけるアッパー、中底、アウトソールの接着工程で使用される揮発性溶剤(プライマー)がスモッグの主要な原因の一つとされています。これを受け、国際的な著名靴ブランドの多くは、製造業者に対し、製造過程で発生する環境コストへの対応を求め始めています。 このような背景のもと、環境負荷を低減しつつ自動化を実現する「ATM3 3Dエアオーロラ自動粗加工装置」は、今後の靴製造プロセスにおいて欠かせない存在です。 本装置の開発目的は、靴製造工程における粗削りおよびプライマー塗布の2段階を置き換えることにあります。当社独自開発の3Dビジュアルスキャンシステムを用いて、靴型ごとに最適なプラズマ処理パスを計算。さらに、内蔵の自動検出・除錯システムにより、処理漏れのあるアッパーを即時に排除することができます。 従来の粗削りと比較し、プラズマ処理によってアッパーと接着剤の間にはより強固な共有結合が形成され、異なる素材間の接着強度が向上します。加えて、自動化システムによりアッパー1足あたりの平均処理速度は10秒に達し、従来の手作業に比べて生産性が飛躍的に向上。さらに、粉塵による汚染リスクも回避できます。