Company introductionwww.ande.com.tw
Business item(s)
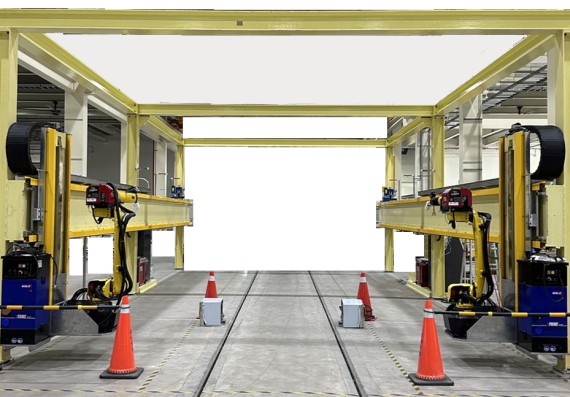
Truss-Type Robotic Welding System With Seam Tracking Sensor For E-Bus Body Assembly
[System Overview] Since the length of the bus is about 12000mm, the width is about 2000mm, and the height is about 2500mm, when the large parts such as the roof frame, chassis, front, rear and left and right side wall frames are assembled and welded separately, it is estimated with a tolerance of ±0.1%. 12000mm exists Tolerance of ±12mm. The bus body can be regarded as a rectangular parallelepiped, which is composed of six sides, that is, it is composed of the above-mentioned major components. Due to tolerances, the left and right side walls are not completely parallel as shown in the design drawing, and the left and right side walls are not ideal either. plane, but may have some angles. For manual welding, these tolerances can be easily corrected by the welder, but for robots, they are far greater than the allowable range. Our innovative equipment represents a ground-breaking achievement and is the world’s first automated welding system specifically designed for electric bus body assembly. It uses the AI artificial intelligence algorithm developed by us and uses a robot equipped with a welding bead tracking sensor to realize fully automatic welding of the electric bus body assembly. After the bus body is pre-assembled in the front-end project, it enters this equipment. Pull up the front and rear isolation belts and confirm that all monitoring signals are normal, then you can start welding with one click. After starting, the robot can independently search for the correct welding position, automatically correct the error, and automatically schedule the welding gun cleaning work according to the number of welds, realizing automated welding of large workpieces, and can achieve welding postures including horizontal welding, vertical welding, and overhead welding. . The main components of the overall system use Ethernet to communicate. For example, the welding bead tracking sensor and the robot control box use 1 Gbps high-speed Ethernet to communicate, which can instantly correct the welding position; left and right Between the side robot control box and the PLC, through the CC-Link IE Field communication interface, all required I/O information can be communicated with each other through this network; the notebook computer can directly modify the welding parameters including welding through the wireless network. Tracking sensor parameters, PLC programs, HMI screens, etc. can also monitor the status of the welding machine. Equipped with a VNC server interface, managers can directly connect to the HMI through the network in the office to check the operating status of the equipment. They can also start welding operations remotely after confirming that the on-site operation is safe. Equipped with MES interface, equipment status, energy consumption information, welding parameters, robot position information, etc. can be connected to the MES system of the customer's factory through the MES interface, and the information can be recorded in the MES system according to customer needs. [Features and Highlights] 1. A world first: Our innovative equipment represents a groundbreaking achievement and is the world’s first automated welding system specifically designed for electric bus body assembly. It uses the AI artificial intelligence algorithm developed by us and uses a robot equipped with a welding bead tracking sensor to realize fully automatic welding of the electric bus body assembly. 2. No need to change the original operating mode: In order to achieve automation in the past, customers often needed to change or adjust the pre- and post-processing methods so that the accuracy of the workpiece could meet the requirements of automation. There is no need to modify the front and rear construction methods after introducing this equipment. Regardless of whether the front-end project is manual work or automatic work, this equipment can be used for welding. 3. No need for precise positioning: After the electric bus body is pre-assembled, there is no need for precise positioning. Welding can be started after the car body is moved to this equipment using the customer's existing rails and transport trolleys. 4. AI artificial intelligence adaptive: The AI artificial intelligence algorithm developed by our company can adjust the welding position, welding gun height, etc. when the vehicle length, height, and width change due to tolerances to maintain stable welding quality. 5. Industry 4.0: Equipped with MES interface, all parameters during vehicle production can be recorded, including welding current, voltage, wire feed speed, welding speed, welding position, energy consumption, etc. With a built-in VNC server, managers can monitor the running status of the equipment directly from the office. [Application benefits] 1. The AI artificial intelligence algorithm developed by our company can not only be applied to the welding of bus body assembly, but also can be applied to the automated welding of large workpieces such as bus roofs and bus side walls. 2. The original manual welding method may have shortcomings such as missed welding, unstable welding quality, insufficient strength, and time consumption. This equipment realizes automatic welding of bus body assembly, ensuring consistent welding quality, saving manpower and improving production efficiency. 3. This equipment has a truss structure. It can also be designed as a robot gantry type or robot slide type structure according to customer needs, providing various customized equipment.

Gantry-type large scale parts assembly robotic resistance spot welding system for railway train
The equipment includes welding guns, welding gun quick change device, robots and ganrty. Large -scale C-type, X-type resistance spot welding guns or resistance series single-sided double-spot welding heads can be used. Manufacturer: Japan DENGENSHA TOA CO., LTD. Welding gun quick change device: Japanese NITTA 500kg ATC, Japanese BL Autotec 700kg ATC or Swiss Staubli 630kg ATC Robot: Japan Fanuc M-900iB/400L 400kg robot Gantry-type equipment: Design and planning by Ander Trading Co., Ltd. Major client: - Taiwan Rolling Stock Co., Ltd. - CRRC Nanjing Puzhen Co., Ltd. - Tianjin CRRC Tangshan Co., Ltd. - Hebei Jingche Rail Transit Vehicles Equipment Co.,Ltd.