Company introductionhttps://www.buffalo-machinery.com/tw/
Business item(s)
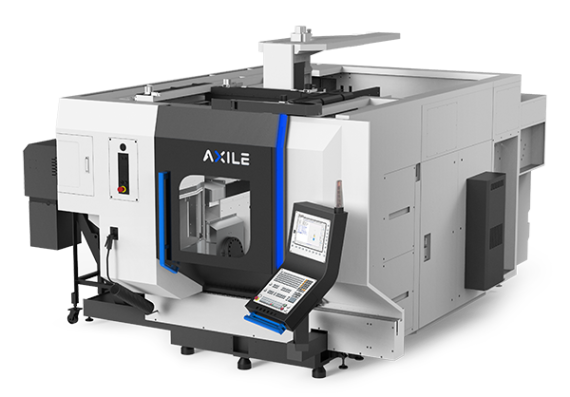
G6 MPC - Motorized Pallet Changer Automation Solution
Available with two or six pallets, AXILE’s automated G6 Motorized Pallet Changer (MPC) exchanges raw workpieces and finished parts via a loading bay at the back side of the machine. Operators can load raw workpieces, and inspect and unload finished parts, while machining continues in the vertical machining center 24/7, dramatically increasing operational efficiency. Freedom and flexibility are core to the design concept, as the MPC solution can be integrated upon initial commissioning of the G6 machine, or at a later stage when production capacity expands. And with the MPC-2 (the two-pallet solution), manufacturers can embrace a Flexible Manufacturing System (FMS), of 12, 24, or 36 pallets total, by integrating one to three machines and two loading stations, depending on the scale required. With AXILE’s digitalized intelligent automation solutions, manufacturers can eliminate production bottlenecks and ramp up production.
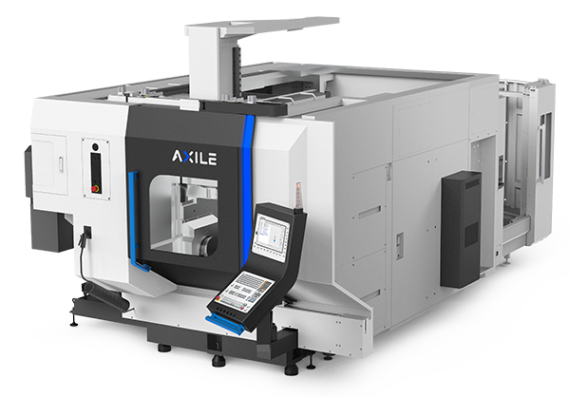
G6 Robotic Pallet Changer (RPC) Automation Solution
AXILE’s automated G6 Robotic Pallet Changer (RPC) solution features a 2-axis robot that keeps machines supplied with workpieces 24/7 from the back side of the machine. Part processing continues simultaneously within the machining center while operators deal with workpieces at the holding area at the back, significantly raising production efficiency to boost throughput.
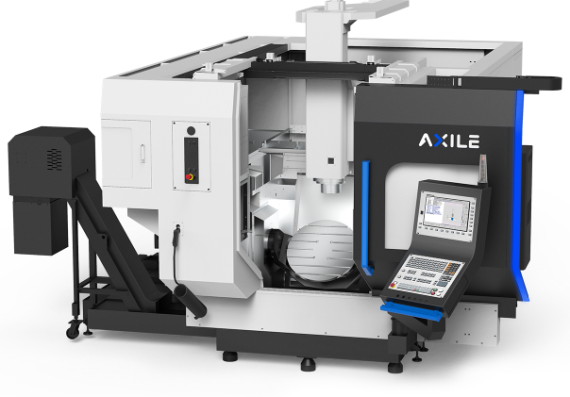
G6 Gantry type 5-axis VMC
With a rotary table diameter of 600 mm, the G6 is a compact vertical machining center designed for agile, smart machining of smaller workpieces requiring complex geometries and intricate features. This highly versatile VMC delivers full 5-axis CNC machining, with the built-in spindle moving along the X,Y,Z-axis, and the table moving in rotary C-axis and swiveling A-axis.
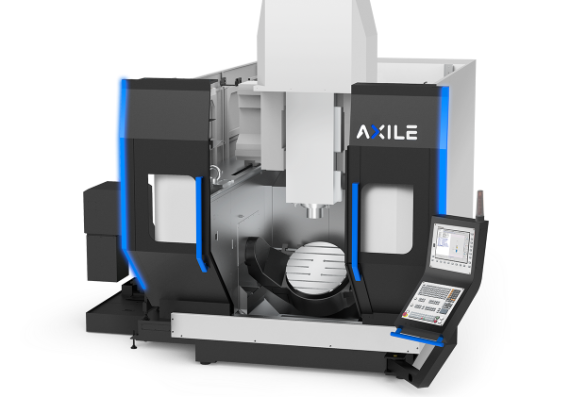
G8 Gantry type 5-axis VMC
The AXILE G8’s powerful gantry design perfectly balances rigidity and precision, ideal for the machining of complex workpieces. With a maximum loading capacity up to 1,300 kg on a swiveling, rotary table, complemented by high-performance built-in spindles, the G8's agility enables production of a wide range of large parts and tools.
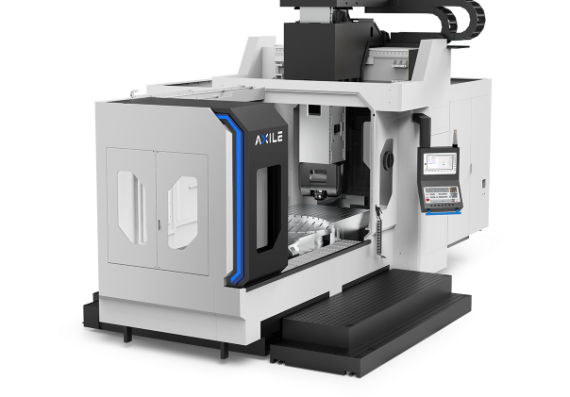
DC12 Double-column type 5-axis VMC
The DC12 is the most robust VMC in AXILE’s arsenal, perfectly suited for handling larger, lengthy workpieces. With a maximum table loading weight of 2.5 tonnes and maximum diameter of 2,200 mm X 1,200 mm, the DC12 takes on the larger, heavier parts common in the aerospace, power generation, and die and mold industries. Its double-column bridge construction allows for greater rigidity, as well as greater control over thermal deformation. As a result, the D12 is capable of deep cuts and complex contouring while maintaining utmost precision.